Charcoal has long been an important commodity in various industries, ranging from water and air filtration, fuel, to cosmetic products. The quality of the charcoal produced heavily depends on the raw materials, and one of the best sources is coconut shell, known for its durability and excellent filtration properties. However, to produce high-quality charcoal, it’s not only about having sufficient raw materials but also the correct ratio between the coconut shell and the resulting charcoal. This is known as the “coconut shell to charcoal ratio,” a concept that plays a crucial role in determining the efficiency and quality of the charcoal produced.
What is the Coconut Shell to Charcoal Ratio?
The coconut shell to charcoal ratio refers to the comparison between the amount of coconut shell used and the amount of charcoal produced during the pyrolysis or burning process. This process involves heating the coconut shells in an oxygen-free environment to produce charcoal, which can be used in various industrial applications.
This ratio is crucial as it determines the production efficiency and the quality of the resulting charcoal. For example, a ratio that is too high or too low can lead to charcoal that is less dense, brittle, or ineffective at absorbing or burning.
In the charcoal manufacturing industry, the commonly used ratios vary depending on the production goals. Typically, the ratio between coconut shells and the resulting charcoal ranges from 3:1 to 5:1, depending on the pyrolysis technique and the temperature applied.
This ratio is important to ensure that every kilogram of coconut shell produces charcoal with optimal quality in terms of durability, density, and absorbency. Understanding and adjusting this ratio correctly can improve production efficiency, reduce raw material waste, and result in higher quality and more cost-effective charcoal.
Read Also: Practical Guide – How to Light Briquettes Without Lighter Fluid
Why is This Ratio Important?
The correct ratio between coconut shells and the charcoal produced is crucial because it directly impacts the quality of the charcoal. The ideal ratio will result in charcoal that has optimal strength, heat resistance, and absorbency. Charcoal made from coconut shells processed with the correct ratio will be denser, more durable, and able to absorb more contaminants in applications such as air or water filtration.
Good charcoal strength also ensures that it lasts longer in its usage, such as when used as fuel for cooking or in the production of activated charcoal. With the correct ratio, the resulting charcoal will be of high quality and meet the specific needs of various industries.
On the other hand, if the ratio between the coconut shells and charcoal is incorrect, the results can be unsatisfactory. A ratio that is too high (too many coconut shells) can produce less charcoal with poor quality, such as fragile or brittle charcoal. Conversely, a ratio that is too low (too few coconut shells) can result in less dense, inefficient charcoal.
In the charcoal industry, especially when using coconut shells as the raw material, this ratio is critical to ensure cost-efficiency and maximize output. The correct ratio will reduce raw material waste, increase productivity, and lower operational costs, all of which are essential in a competitive market.
How to Calculate the Coconut Shell to Charcoal Ratio
To calculate the correct coconut shell to charcoal ratio, follow these steps:
- Weigh the amount of coconut shells that will be used in the charcoal production process.
- Perform the pyrolysis or burning process on the coconut shells.
- After the pyrolysis process is complete, weigh the amount of charcoal produced.
- The ratio is calculated by comparing the weight of the coconut shells used with the weight of the charcoal produced. For example, if you use 5 kilograms of coconut shells and produce 1 kilogram of charcoal, the coconut shell to charcoal ratio is 5:1. This calculation helps determine the efficiency of the burning process and the quality of the charcoal produced.
Important Factors Affecting the Ratio
Several key factors influence the calculation of the coconut shell to charcoal ratio, including the size and type of coconut shell, the pyrolysis technique used, and the burning process.
Size of Coconut Shell
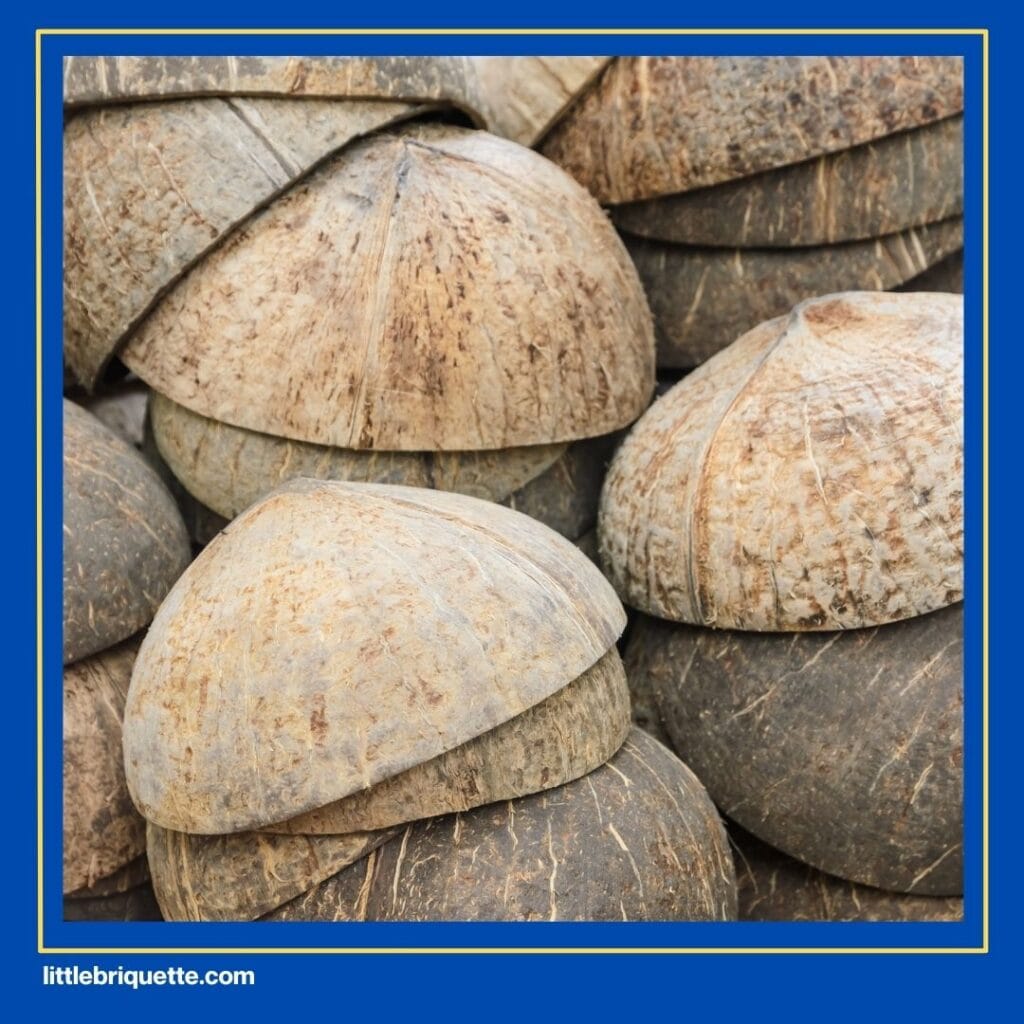
The size of the coconut shell is the first factor that affects the coconut shell to charcoal ratio calculation. Larger coconut shells tend to produce less charcoal compared to smaller shells. This is due to variations in the structure and composition of the material in each coconut shell.
Larger shells require longer burning times to oxidize all parts of the material, and because of their thickness, some of the material may not fully convert into charcoal. In contrast, smaller, thinner coconut shells burn faster, resulting in more charcoal produced more efficiently. Therefore, it is important to consider the size of the coconut shell when determining the correct ratio to produce high-quality charcoal.
Pyrolysis Technique
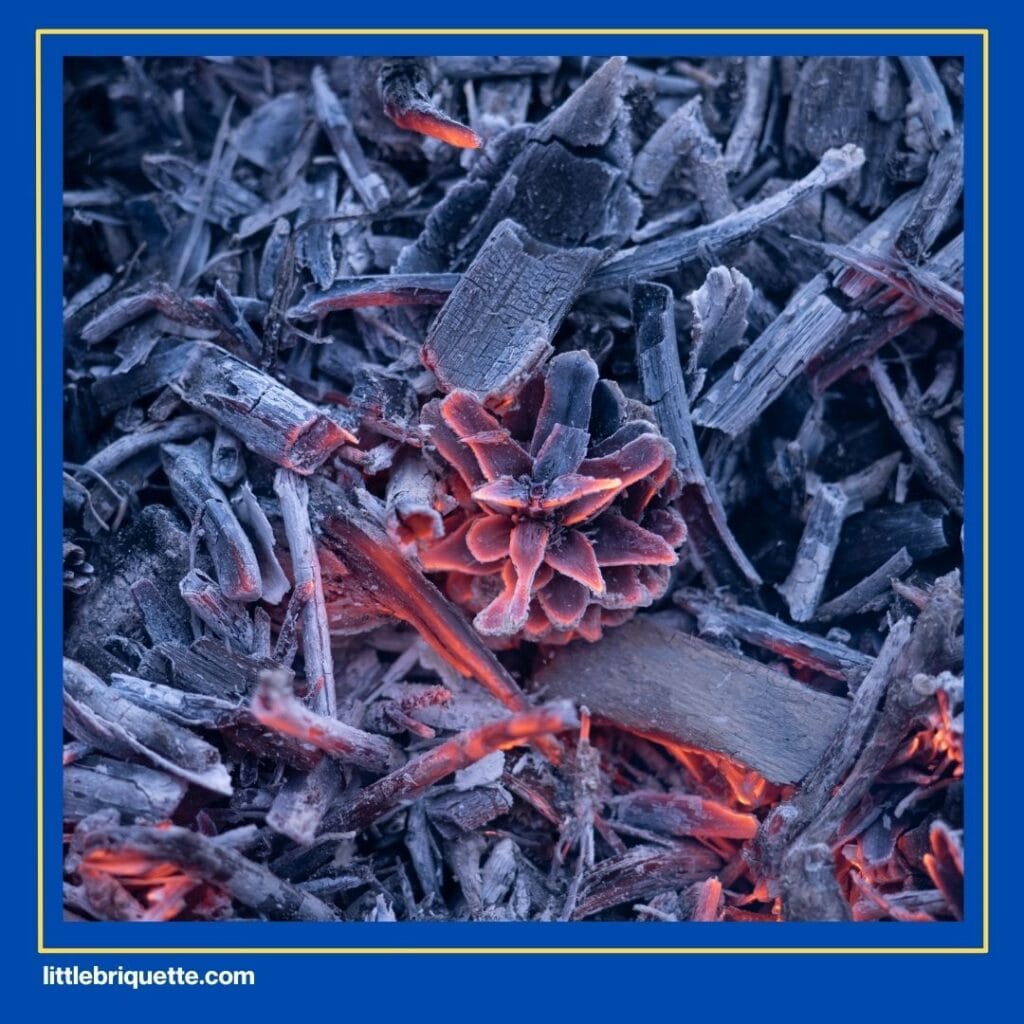
The pyrolysis technique, or the oxygen-free burning process, is used to transform organic materials, such as coconut shells, into charcoal by heating in a controlled environment. This process involves heating the coconut shells at high temperatures in a closed space, without oxygen, to prevent direct combustion.
During pyrolysis, the high temperature causes the coconut shells to decompose into gas, liquid, and charcoal. The charcoal produced has denser properties and is more effective, especially for applications such as filtration or as a fuel. This pyrolysis technique can be performed in various ways, including traditional kilns or more modern and efficient pyrolysis reactors.
Burning Time and Applied Temperature
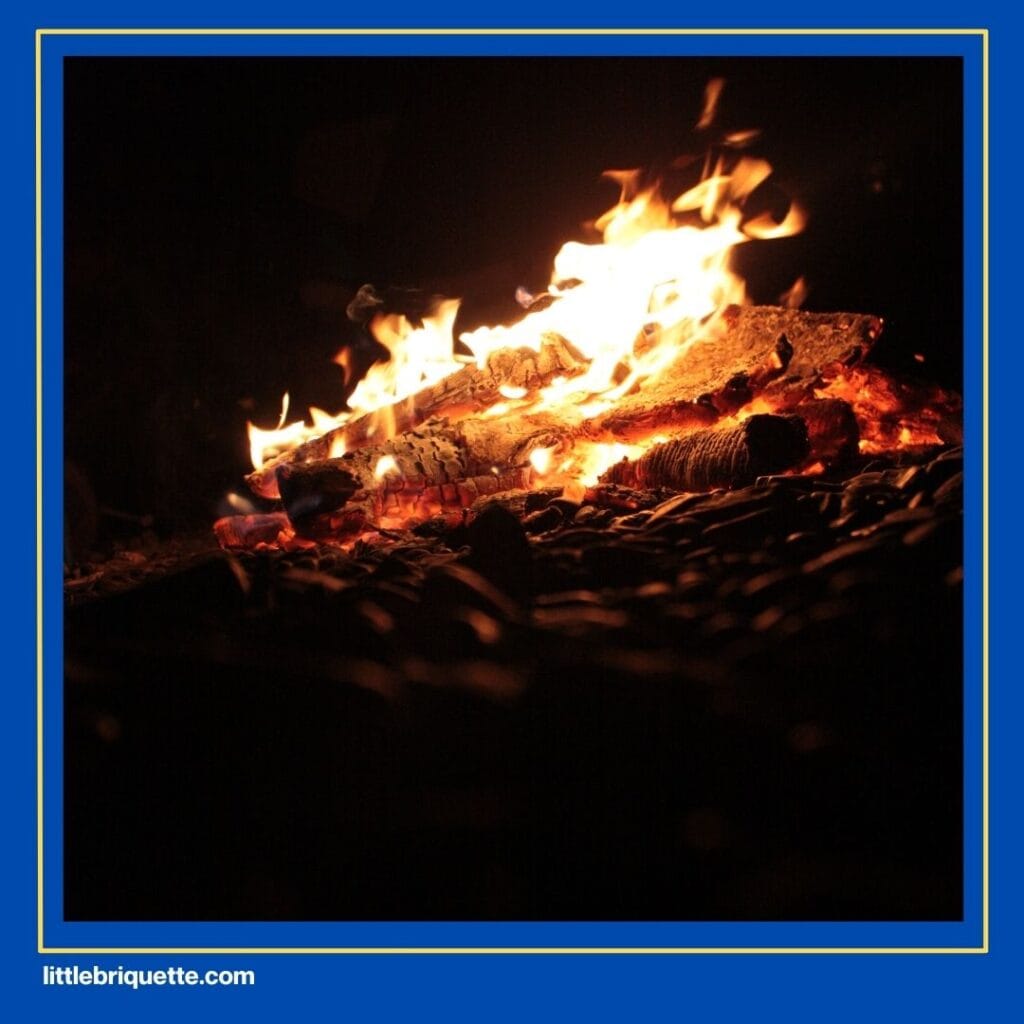
A burning time that is too short can result in charcoal with low density, which means it will have poor absorbency and suboptimal quality. On the other hand, if the burning time is too long, much of the carbon in the coconut shell will oxidize into gas, reducing the amount of charcoal produced. Ideally, the burning time should be adjusted according to the size and type of coconut shell used and the final purpose of the charcoal production. Therefore, controlling the burning duration is crucial to ensure that each process produces dense and efficient charcoal.
The applied temperature also plays a significant role in the pyrolysis process. At low temperatures, the decomposition of organic material proceeds slowly, and the resulting charcoal tends to have high moisture content and low strength. However, if the temperature is too high, while the process is faster, it may lead to excessive burning, which reduces the quality of the charcoal.
The ideal temperature range for pyrolyzing coconut shells is between 400°C to 600°C, depending on the technique used. Within this temperature range, the coconut shells efficiently convert into high-quality charcoal, with good heat resistance and optimal absorbency. Therefore, precise temperature control is crucial to obtaining charcoal with the desired characteristics.
Read Also: Understanding the Content of Coconut Charcoal Briquettes
Best Quality Coconut Charcoal Briquettes
It is important to understand the quality of the coconut charcoal briquettes as they have a significant impact on health and optimal cooking results. To obtain the best quality coconut charcoal briquettes, you can purchase directly from Little Briquette by contacting the admin through the provided number.